The Advanced SiC Cantilever Paddle for Wafer Processing created by vet-china provides an excellent solution for semiconductor manufacturing. This cantilever paddle is made of SiC (silicon carbide) material, and its high hardness and heat resistance enable it to maintain excellent performance in high temperature and corrosive environments. The design of the Cantilever Paddle allows the wafer to be reliably supported during processing, reducing the risk of fragmentation and damage.
SiC Cantilever Paddle is a specialized component used in semiconductor manufacturing equipment such as oxidation furnace, diffusion furnace, and annealing furnace, the main use is for wafer loading and unloading, supports and transports wafers during high-temperature processes.
Common structures of SiC cantilever paddle: a cantilever structure, fixed at one end and free at the other, typically has a flat and paddle-like design.
VET Energy use high purity recrystallized silicon carbide materials to guarantee the quality.
Physical properties of Recrystallized Silicon Carbide |
|
Property |
Typical Value |
Working temperature (°C) |
1600°C (with oxygen), 1700°C (reducing environment) |
SiC content |
> 99.96% |
Free Si content |
< 0.1% |
Bulk density |
2.60-2.70 g/cm3 |
Apparent porosity |
< 16% |
Compression strength |
> 600 MPa |
Cold bending strength |
80-90 MPa (20°C) |
Hot bending strength |
90-100 MPa (1400°C) |
Thermal expansion @1500°C |
4.70 10-6/°C |
Thermal conductivity @1200°C |
23 W/m•K |
Elastic modulus |
240 GPa |
Thermal shock resistance |
Extremely good |
The advantages of VET Energy’s Advanced SiC Cantilever Paddle for Wafer Processing are:
-High temperature stability: usable in environments above 1600°C;
-Low thermal expansion coefficient: maintains dimensional stability, reducing wafer warpage risk;
-High purity: lower risk of metal contamination;
-Chemical inertness: corrosion-resistant, suitable for various gas environments;
-High strength and hardness: Wear-resistant, long service life;
-Good thermal conductivity: helps in uniform wafer heating.
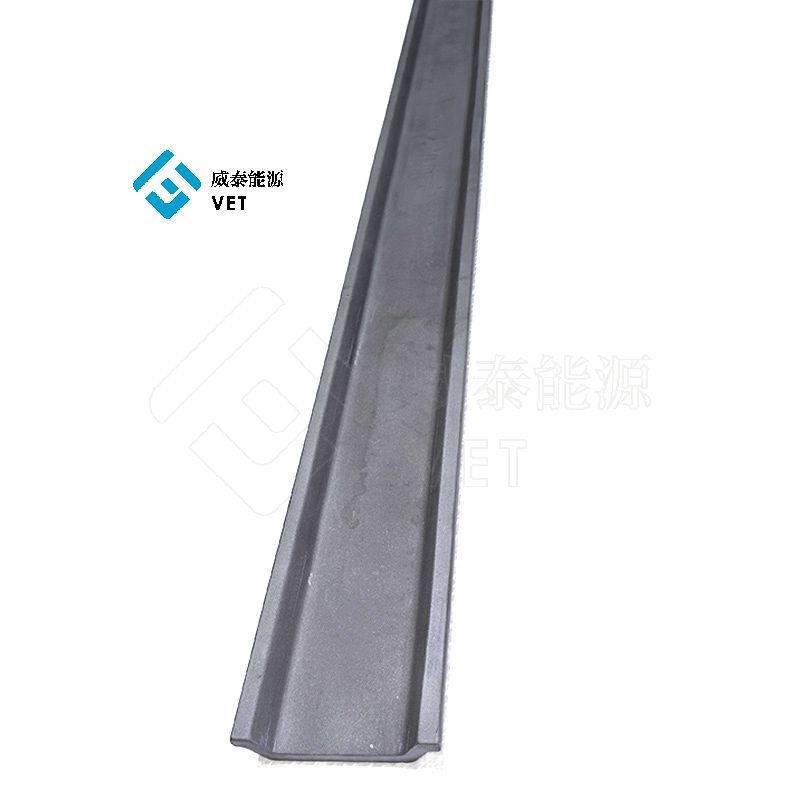
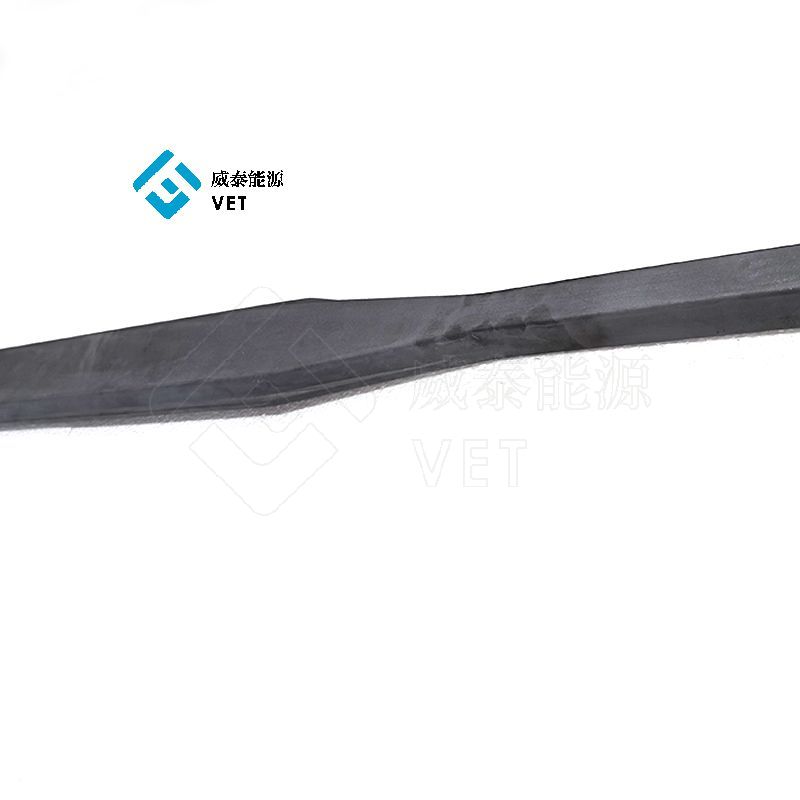
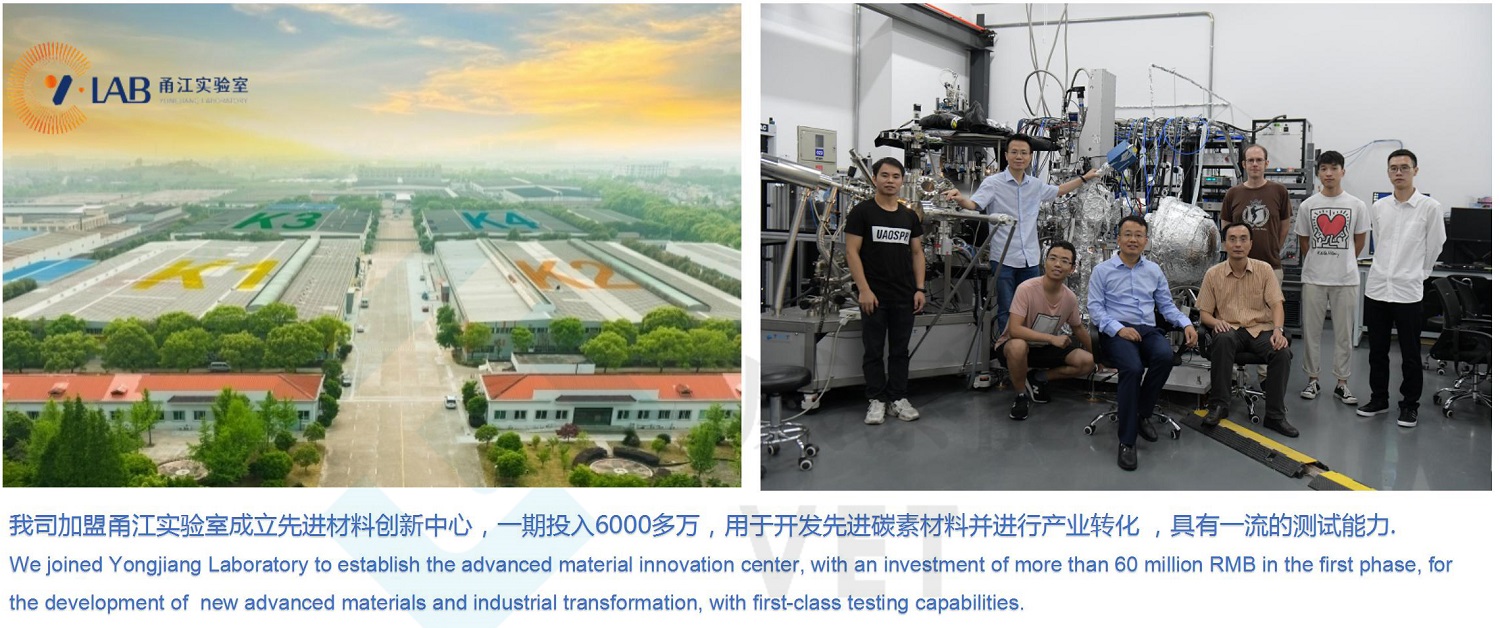
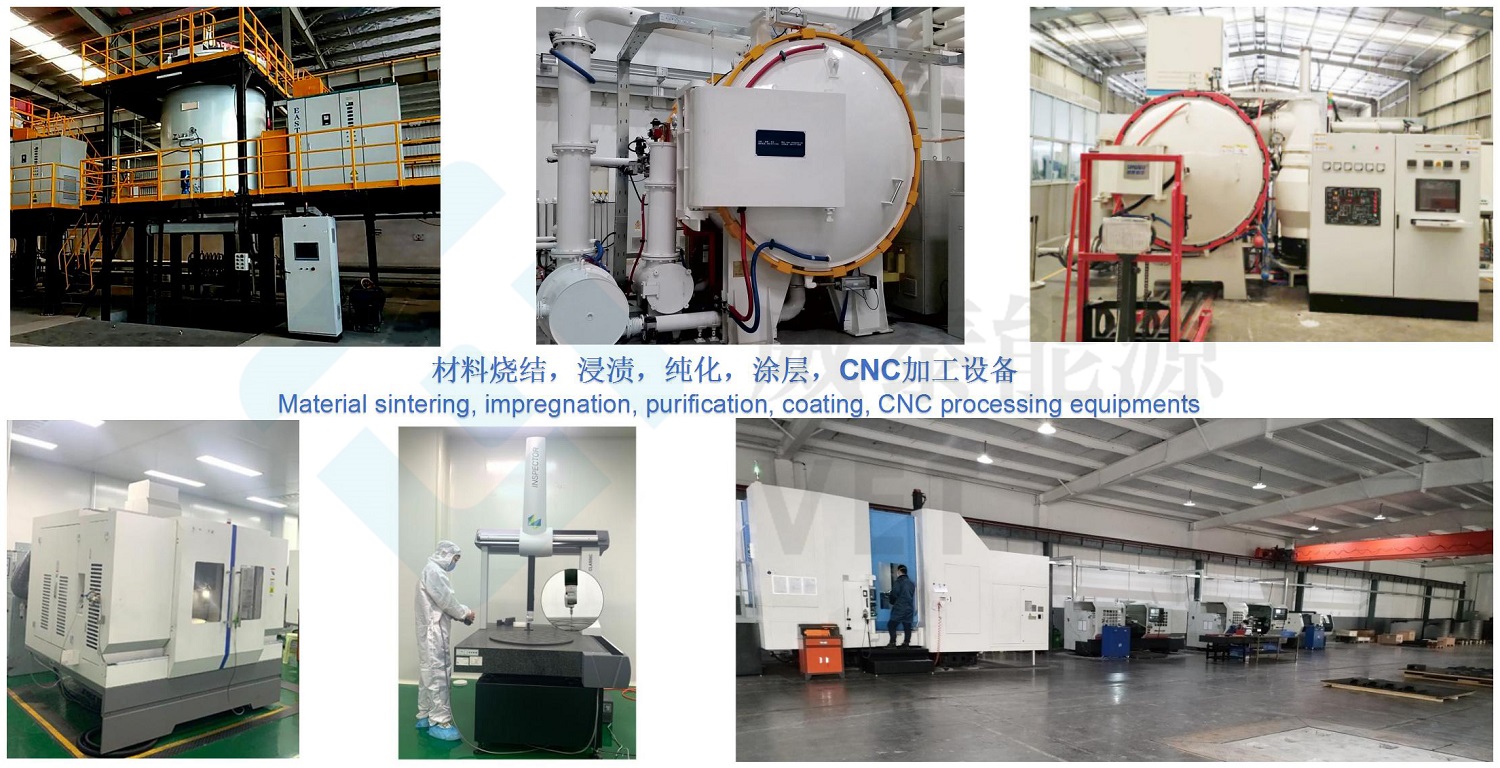
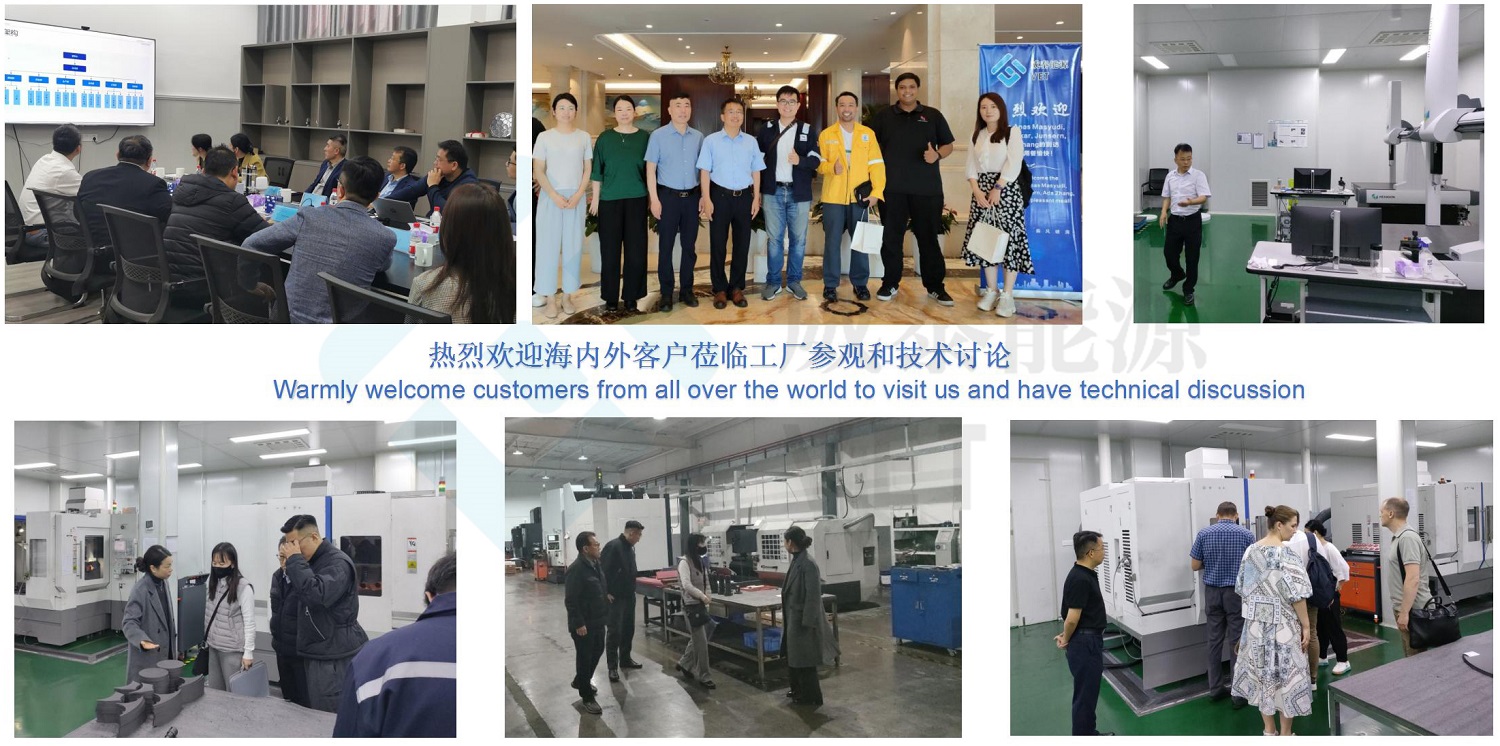